Recognizing the Plastic Injection Molding Refine for High-Quality Production
Recognizing the Plastic Injection Molding Refine for High-Quality Production
Blog Article
Secret Advantages of Utilizing Plastic Injection Molding in Manufacturing
Plastic shot molding has actually emerged as a critical strategy in the manufacturing industry, supplying a variety of advantages that dramatically boost production processes. Noteworthy benefits consist of exceptional production efficiency, the capacity for elaborate layouts, and a positive price structure that appeals to services of all dimensions.
High Manufacturing Efficiency
Among one of the most significant benefits of plastic shot molding is its high production effectiveness, which can result in the rapid manufacturing of hundreds of identical components within a short duration. This efficiency is mostly credited to the automatic nature of the injection molding process. When the first setup and mold and mildew production are finished, the production of parts can be scaled up considerably without a matching increase in labor expenses or time.
The process commonly entails heating plastic pellets up until they melt, infusing the molten product right into a precisely designed mold and mildew, and enabling it to strengthen and cool down - Plastic Injection Molding. This cycle can be completed in simple seconds to minutes, depending on the complexity and dimension of the component being produced. Because of this, manufacturers can accomplish high outcome rates, making plastic injection molding a perfect choice for mass production
In addition, the capacity to create huge amounts regularly makes certain reduced unit prices, making it a cost-effective option for organizations. This manufacturing efficiency not just fulfills market demands promptly however also improves the general competition of producers in different industries. Subsequently, plastic shot molding stays a preferred technique for high-volume production applications.
Layout Adaptability
The capabilities of plastic injection molding prolong past high manufacturing effectiveness to incorporate significant style adaptability. This manufacturing process allows developers and designers to develop elaborate and intricate shapes that could be challenging or difficult to achieve with various other approaches (Plastic Injection Molding). The capability to conveniently customize and adjust mold and mildew layouts suggests that producers can quickly reply to changing market demands and innovate new item styles without considerable retooling
In addition, plastic shot molding sustains a vast array of products, including various thermoplastics and thermosetting polymers. This selection allows the production of elements with special residential properties, such as enhanced stamina, light-weight characteristics, or specific thermal and electrical features. Furthermore, the process permits for the combination of several features right into a solitary part, decreasing the need for setting up and minimizing prospective factors of failing.
The precision of injection molding also ensures that elements are created with limited resistances, improving fit and function. The flexibility to produce little to huge sets efficiently additionally emphasizes its versatility, making it an ideal selection for both prototyping and large manufacturing. Generally, design adaptability is a cornerstone benefit of plastic injection molding, driving development in numerous markets.
Cost-Effectiveness
Cost-effectiveness attracts attention as a substantial benefit of plastic shot molding in production. This procedure permits the mass production of top notch plastic parts at a reasonably affordable per unit, particularly when contrasted to various other manufacturing methods. The performance of injection molding depends on its capability to generate complex shapes with minimal waste, maximizing material usage and decreasing total expenditures.
Furthermore, the speed of manufacturing is a critical consider cost-effectiveness. When the preliminary mold is developed, the moment called for to generate each subsequent component is dramatically lowered, leading to enhanced output and faster turnaround times. This quick production ability not just meets high-volume demands but also decreases labor prices, as automated systems can deal with much of the process.
Furthermore, the durability and long life of injection-molded items add to their cost-effectiveness in time. These parts typically require less maintenance and replacement, causing lower lifecycle prices for end-users and manufacturers alike. In recap, the cost-effectiveness of plastic injection molding makes it an attractive option for businesses looking for to boost their production performance while maintaining product high quality.
Material Convenience
Product versatility is a characteristic of plastic shot molding, enabling makers to choose from a large variety of polymers that satisfy particular performance needs. This flexibility allows for the manufacturing of parts customized to numerous applications, ranging from automotive parts directory to customer products.
Generally made use of materials consist of acrylonitrile butadiene styrene (ABS), polycarbonate (COMPUTER), and polypropylene (PP), each offering one-of-a-kind properties such as influence resistance, heat resistance, and chemical security. Makers can choose products based upon attributes like stamina, weight, and thermal stability, guaranteeing the end product meets functional and aesthetic demands.
Furthermore, the capability to integrate different polymers through co-injection strategies more improves product convenience. This permits the development of multi-layered components with distinct characteristics, such as soft-touch surfaces combined with rigid structural components.
Additionally, advancements in recycled and biodegradable products are broadening the options offered, straightening with sustainability goals in manufacturing. On the whole, the diverse material options in plastic injection molding encourage suppliers to introduce and enhance their items, promoting the advancement of extremely specialized and competitively useful services.
Enhanced Item Resilience
Improved item resilience is one of the substantial benefits supplied by plastic injection molding, as the manufacturing process permits for exact control over product residential or commercial properties and element style. This accuracy ensures that the end products show improved mechanical stamina and durability, which are crucial consider a series of applications, from consumer items to commercial elements.
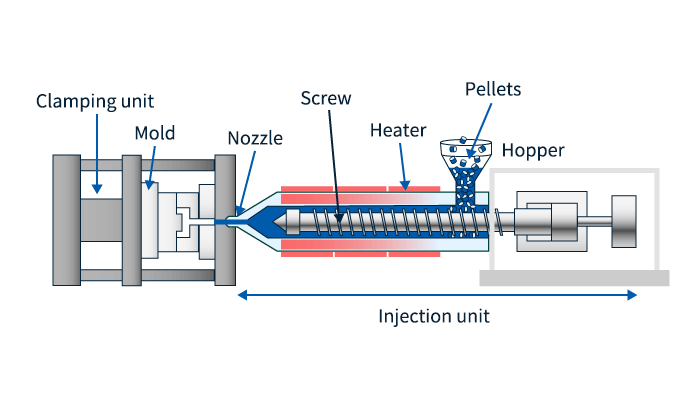
Furthermore, the intricate geometries possible with shot molding allow the production of components that can hold up against stress and pressure much better than traditional manufacturing methods. The consistent wall surface thickness and minimized product waste also add to the total integrity of the product, minimizing the opportunities of failure throughout its lifecycle.
Verdict
In verdict, plastic injection molding provides significant advantages in production, including high manufacturing effectiveness, design flexibility, and cost-effectiveness. These factors collectively establish plastic injection molding as an optimal remedy for mass production applications, addressing the vibrant requirements of modern manufacturing atmospheres.
Plastic shot look at this website molding has emerged as a critical strategy in the manufacturing field, supplying a variety of benefits that considerably enhance production processes.One of the most substantial advantages of plastic shot molding is its high manufacturing performance, which can result in the rapid manufacturing of thousands of the same parts within a short timeframe. Plastic Injection Molding.The capacities of plastic shot molding expand past high production Going Here performance to encompass significant design versatility.In conclusion, plastic shot molding presents substantial benefits in manufacturing, consisting of high production performance, style adaptability, and cost-effectiveness. These variables jointly develop plastic shot molding as an ideal service for mass manufacturing applications, resolving the vibrant needs of modern manufacturing settings
Report this page